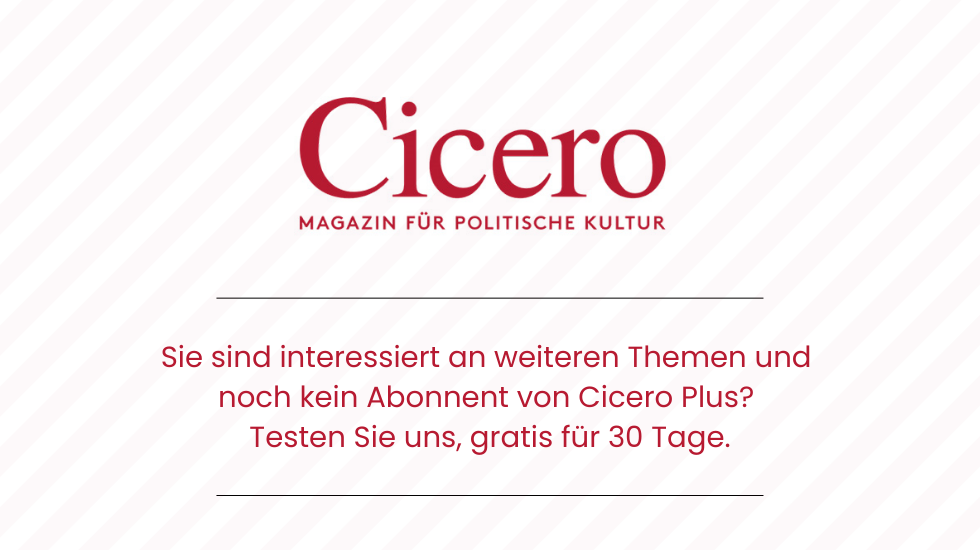
- Druck dir deinen Büstenhalter!
Mit 3D‑Druckern kann jeder alles produzieren: Tassen, Prothesen, Waffenteile oder Toastbrot. Aber bis zur Massentauglichkeit ist es noch ein weiter Weg
Vielleicht können wir in ein paar Jahren alle morgens eine halbe Stunde länger schlafen, weil keiner mehr das Frühstück vorbereiten muss. Einfach den Rechner hochfahren, auf dem Monitor „Spiegelei und Toast“ auswählen und auf „drucken“ klicken. Aus dem 3D‑Printer auf dem Frühstückstisch kommt dann wenig später das Essen. Wer vorher seine dritten Zähne verlegt hat, kann auch sein Gebiss auf diese Weise reproduzieren. Kein frisch gebügeltes Hemd zur Hand? Die Lesebrille zerbrochen? Kein Problem, der heimische 3D‑Drucker schafft das.
Derzeit läuft ein Hype um die „next trillion dollar industry“, der solche Szenarien erzeugt. Er wird vor allem aus Amerika befeuert. Der bekannte US-Ökonom Jeremy Rifkin erwartet von der 3D‑Drucktechnik nicht weniger als die nächste industrielle Revolution. Tatsächlich lassen sich heute schon Gegenstände wie Legosteine, Tassen oder Armbänder ausdrucken. Im Alltag sind 3D-Drucker jedoch längst noch nicht angekommen.
Raum 2014 der Rheinisch-Westfälischen Technischen Hochschule Aachen. Bevor die Revolution beginnen kann, müssen in der Gegenwart noch ein paar Sonderwünsche abgearbeitet werden. „René is the Fab Lab Master“ steht an der Tür, denn dahinter liegt das Reich des Informatikers René Bohne – etwa so groß wie eine Stehküche, aber vollgestellt mit modernen Apparaturen. „Fab Lab“ steht für Fabrication Laboratory, das Aachener war das erste seiner Art in Deutschland und wurde 2009 von Bohnes Professor Jan Borchers eröffnet. Die Idee zu den „Fab Labs“ kommt aus den USA. Unter Aufsicht und mithilfe der Wissenschaftler soll jeder die Möglichkeit haben, neueste Technologien auszuprobieren.
[gallery:Merkel looking at technical things]
In Aachen geht das jeden Dienstag. Gerade nutzt Andreas Gottswinter das Angebot, ein 26 Jahre alter Maschinenbaustudent mit dem Schwerpunkt Luftfahrt. Er möchte einen Fanartikel aus dem Science-Fiction-Film „Avatar“ nachbauen: ein schwarzes Gehäuse mit dem Durchmesser einer CD, das mithilfe von Elektromagneten eine Plastikplakette in der Luft schweben lässt. Die Elektronik sei fast fertig, das Aluminiumgehäuse lasse er sich von Freunden gießen, erzählt er, nur diese dreidimensionale schwarze Plakette fehle ihm noch.
René Bohne hört zu und nickt. Diese Aufgabe stellt für seinen 3D‑Drucker kein Problem dar. „Er ist der Star hier“, sagt Bohne. Ihm gegenüber führen die hochpräzisen Laserschneider, die empfindlichen Geräte für Strommessungen oder eine Fräse, mit der man elektronische Leiterplatten herstellen kann, ein Schattendasein. Der Drucker steht hinten links, schwarz, so groß wie ein Kühlschrank. Er kostet rund 40 000 Euro und wiegt 140 Kilogramm. Drinnen im Gehäuse befindet sich der Druckkopf, der sich auf drei Achsen frei bewegen kann: Breite, Länge und Höhe. Das Gehäuse selbst, in dem gedruckt wird, ist gerade mal 30 Zentimeter hoch und 20 Zentimeter breit und lang. Über eine Spule zieht ein Motor dünnen Plastikdraht in den Druckkopf; der durch Wärme verflüssigte Kunststoff wird dann in Schichten auf eine Trägerplatte aufgetragen, langsam, Lage für Lage.
Nächste Seite: Noch nimmt ein einfacher Druck jede Menge Zeit in Anspruch
Wenn der Druckkopf nach rechts und nach links fährt, surrt das Gerät wie ein Tintenstrahldrucker in den achtziger Jahren. Bei den besten Geräten sind die Lagen nur einen Zehntelmillimeter dick. Nur so kann der Kunststoff schnell genug aushärten und gleichzeitig die notwendige Präzision erzielt werden. Der Nachteil ist, dass selbst der Druck kleiner Gegenstände noch sehr viel Zeit in Anspruch nimmt.
Vorher schauen sich Bohne und Gottswinter auf dem Rechner die 3D‑Grafik an, die der „Avatar“-Fan mitgebracht hat. Sie berechnen, wie viel Plastik sie brauchen werden: Am Ende wird Gottswinter 37 Euro für den 14 Stunden dauernden 3D‑Ausdruck seiner 76 Kubikzentimeter großen Plakette zahlen. Dass er noch Wochen auf sie warten muss, weil René Bohne zunächst noch andere Wünsche zu erfüllen hat, ist kein Problem. „Eilt überhaupt nicht“, sagt er. Hier hat die Revolution noch Zeit.
Der Drucker im Aachener Fab Lab ist vom deutschen Wohnzimmer noch weit entfernt, aber Bohne erfüllt nicht nur jeden Dienstag Hobbytüftlern ihre Sonderwünsche. Mit anderen Maschinenbauern und Designern bastelt er an kleinen, günstigeren Geräten, die nicht größer sind als eine Mikrowelle: Sie arbeiten teilweise ohne Gehäuse, zusammengeschraubt nur aus Metallstangen, ein paar Metern Kabel und ein bisschen Elektronik – auf den ersten Blick ein selbst gebautes Spielzeug von Hobbytüftlern. Materialwert: ein paar Hundert Euro.
[[nid:53856]]
Das Prinzip ist bei jedem 3D‑Drucker dasselbe: Die Geräte machen aus Bits Atome. Aus einer 3D‑Grafikdatei entstehen fertige Gegenstände – ein Becher, ein Gewinde oder ein Bauklötzchen. Es muss nicht immer Plastik sein, all das ist eine Frage des Geräts, der Größe und des Geldes. Es gibt bereits Drucker, die Herzklappen, komplette Kugellager, Waffenteile und Querflöten drucken können. Im Auftrag der US-Raumfahrtbehörde Nasa arbeiten Forscher an 3D‑Food-Printern, um den Speiseplan der Astronauten bei längeren Weltraummissionen abwechslungsreicher zu gestalten.
Die Industrie nutzt bereits seit 25 Jahren 3D‑Drucker für den Bau von Prototypen oder für individuelle Modelle in der Medizintechnik. Diese Drucker arbeiten mit der sogenannten Sintertechnik und fangen bei 250 000 Euro an. Bei dieser Technik schmelzen Laser das Material, Schieber tragen die dünnen Schichten gleichmäßig auf. Nach jeder Schicht senkt sich die Trägerplatte ab, damit die nächste Schicht aufgetragen werden kann. Der größte Vorteil der Sintertechnik besteht darin, dass neben Kunststoffen auch verschiedene Metalle, darunter Stahl, bearbeitet werden können. In Deutschland sitzt mit Eos der weltweit führende Hersteller solcher Anlagen.
Für Massenproduktionen lohnen sich diese Drucker aber nicht, weil sie jedes Teil einzeln drucken und langsamer sind als das bei Großserien gängige industrielle Spritzgussverfahren.
Während deutsche Firmen wie Eos, SLM oder FKM vor allem auf die Produktion und Weiterentwicklung von Industriedruckern mit Sintertechnik setzen, ist das Marktpotenzial von 3D‑Druckern für private Endverbraucher in Deutschland noch schwer einzuschätzen.
Nächste Seite: Schon 2007 kam der erste 3D-Drucker für Heimwerker
Der Berliner Bernhard Voslamber hat sich allerdings bereits 2004 eine kommerzielle Nische gesucht. Er ist einer von vielen kleineren Anbietern, die für Privatkunden, Designer, Architekten oder mittelständische Betriebe 3D‑Druck als Dienstleistung anbieten. Zwischen 40 und 8000 Euro verlangt er für einen Ausdruck: Von Ersatzteilen bis zu Kleinserien oder dem tischgroßen Architekturmodell eines ganzen Straßenzugs bietet er alles an. Voslamber, 44 Jahre alt, nennt sich selbst einen „Einzelkämpfer“. In seiner Firma Objectplot in Berlin-Charlottenburg stehen zwei Drucker, einen dritten hat er sich in den USA bestellt. Die 80 000 Euro hat er schon überwiesen. Doch die Lieferung verzögert sich um einen Monat. Langsam wird er nervös, „die Aufträge nehmen ständig zu“. Mit dem neuen Drucker wird er weitere Materialien drucken können, wie Gummidichtungen oder durchsichtige Designer- oder Shampoo-Flaschen. An die Massentauglichkeit des 3D‑Drucks oder gar eine Revolution glaubt Voslamber trotz gestiegener Nachfrage nicht: „Für die Industrie wird sich das nie lohnen. Die Nachfrage von ein paar Designern und Freiberuflern und die Produktion von Kleinserien können externe Dienstleister befriedigen.“
Die Idee, die 3D‑Drucktechnik für Normalbürger zu öffnen, entstand in den USA. 2007 kam dort mit dem Reprap der erste 3D‑Drucker für Heimwerker auf den Markt. Es war ein Open-Source-Projekt, bei dem viele Tüftler online zusammenarbeiteten und ihre Baupläne offenlegten. Das Ziel war ein Drucker, der seine eigenen Bestandteile selbst reproduzieren kann. Das Gerät sollte möglichst günstig sein, damals kostete es rund 1000 Euro. Heute können Bastler eine solche Kiste mit ein paar Metallstangen und etwas Technik in ein paar Stunden zusammenbauen.
[gallery:Das Auto - des Deutschen liebstes Spielzeug]
Aus dem Reprap entstand die Firma Makerbot. Ihr geht es weniger um den günstigsten Preis als um technische Zuverlässigkeit. Das neueste Modell, den Replicator 2, gibt es ab 1800 Euro zu kaufen, Abnehmer sind bisher vor allem Architekten und Produktdesigner. Mit Thingiverse hat Makerbot einen eigenen Online-Marktplatz für 3D‑Vorlagen geschaffen. Viele Tüftler sind enttäuscht, dass aus dem Open-Source-Projekt ein Produkt wurde, und bauen weiterhin lieber ihre eigenen Drucker. Dem Wachstum schadet das nicht: Der Verkauf privater 3D‑Drucker in den USA stieg von 5000 Stück im Jahr 2010 auf 23 000 ein Jahr später.
Längst gibt es große Player auf dem Markt. Neben Makerbots oder dem Druckerhersteller Stratasys zählt dazu auch Shapeways, eine einst niederländische Firma, die ihren Hauptsitz nach New York verlegt hat. Bei Shapeways können Kunden ihre 3D‑Grafiken hochladen oder Drucke von Vorlagen bestellen, Lieferzeit: zehn Tage. Laut Shapeways existieren aktuell sechs Milliarden Muster an 3D‑Vorlagen.
Autoren wie Chris Anderson, ehemaliger Chefredakteur des US-Technik-Magazins Wired, vergleichen den 3D‑Druck dagegen mit der Erfindung des Spinnrads im 18. Jahrhundert oder dem Beginn der Massenproduktion im 19.Jahrhundert. Sein Buch „Makers“ ist gerade auf Deutsch erschienen. Während die Digitalisierung immer noch nur einen Teil der Warenwelt betreffe, würden nun aus Dateien physische Waren. Der Konsument bekomme die Hoheit: Er sei nicht mehr auf das vorhandene Warenangebot angewiesen. Kenntnisse in 3D‑Grafikprogrammen wie Cad oder Vorlagen anderer Designer im Internet reichten. Auch Erfinder oder Produktdesigner könnten in Zukunft Ideen schneller realisieren, weil sie nicht länger nach Unternehmen suchen müssten, die ihre Entwürfe herstellen. Diese Produktion könnten in Zukunft Plattformen wie Thingiverse oder Shapeways übernehmen, mit denen sich ein Designer dann die Einnahmen teilt.
Nächste Seite: Der Weg zum Massengeschäft ist noch weit
Sollten in ein paar Jahren tatsächlich in fast jedem Haushalt zumindest kleinere 3D‑Drucker stehen, könnte das die Herstellung von Alltagsprodukten radikal verändern. Die Auswirkungen können die betreffenden Branchen am Niedergang der klassischen Medienunternehmen und der Musikindustrie studieren, die seit Beginn der flächendeckenden Digitalisierung weiterhin auf der Suche nach neuen, funktionierenden Geschäftsmodellen sind.
So wie sich die Musikindustrie gegen MP3-Raubkopien zu wehren versucht, kämpft der Spielzeughersteller Lego gegen das illegale Nachdrucken seiner Steine, die aus ABS-Kunststoff sind, demselben Material, das auch zahlreiche 3D‑Drucker verwenden. Gleichzeitig versucht Lego vom 3D‑Hype zu profitieren und bietet seinen Kunden online an, eigene, individuelle Steine zu entwerfen und diese dann bei Lego in Auftrag zu geben.
Der Weg zum Massengeschäft scheint aber weit. Noch kostet eine Kartusche mit 1000 Kubikzentimetern ABS-Kunststoff-Draht 500 Euro. Dabei ist der Materialwert maximal ein Zehntel. Die Spezialanbieter sind häufig Monopolisten. Doch immer mehr Unternehmen drängen in den 3D‑Markt, sodass die Preise für Geräte und Material fallen werden.
Auf dem Campus der Freien Universität Berlin sitzt eine der jüngsten Firmen der Branche. Drei junge Wissenschaftler haben hier einen Raum bezogen und mithilfe der Universität Trinckle gegründet. Seit ein paar Tagen ist eine Testversion der Internetseite online. Sie wollen – ähnlich wie Shapeways – einen Druckservice und einen Marktplatz für 3D‑Vorlagen bieten.
[[nid:53772]]
Als Firmensitz dient dem Diplom-Kaufmann Florian Reichle und den promovierten Physikern Marlene Vogel und Gunnar Schulze fürs Erste ein Zimmer im Gebäude L, im sechsten Stock, wo die Lampen nicht richtig gehen und nebenan die Universitätsverwaltung sitzt. Die drei haben viele Ideen, sprechen von einem „App-Store für 3D‑Druck“ und von „social manufacturing“. Den 60 000-Euro-Drucker, der auch farbig drucken kann, müssen sie sich aber immer noch vom Professor ausleihen.
Potenzielle Investoren hätten beim Thema 3D‑Drucker anfangs abgewunken; das habe sich nun geändert. Doch sie wissen auch, dass ein Hype seine Tücken hat. Florian Reichle zeigt auf ein grünes Plastikarmband auf dem Tisch, das aus dem 1000-Euro-Drucker stammt. „Wenn man einem das jetzt als die industrielle Revolution verkauft – dann denkt der auch: na ja.“
Bei älteren Beiträgen wie diesem wird die Kommentarfunktion automatisch geschlossen. Wir bedanken uns für Ihr Verständnis.